[Nikko Kasei] Pushing the limits of molding by combining diverse ideas and skills
Molding process requires excellent "molding technology" and "die technology". As an OEM manufacturer of "home appliance parts" and "automotive parts," Nikko Kasei has been required to maintain strict quality control under any environmental changes. Nikko Kasei is also challenging the limits of molding by combining unique technologies of "design" and "material development" and investing in an AI-equipped injection molding machine.
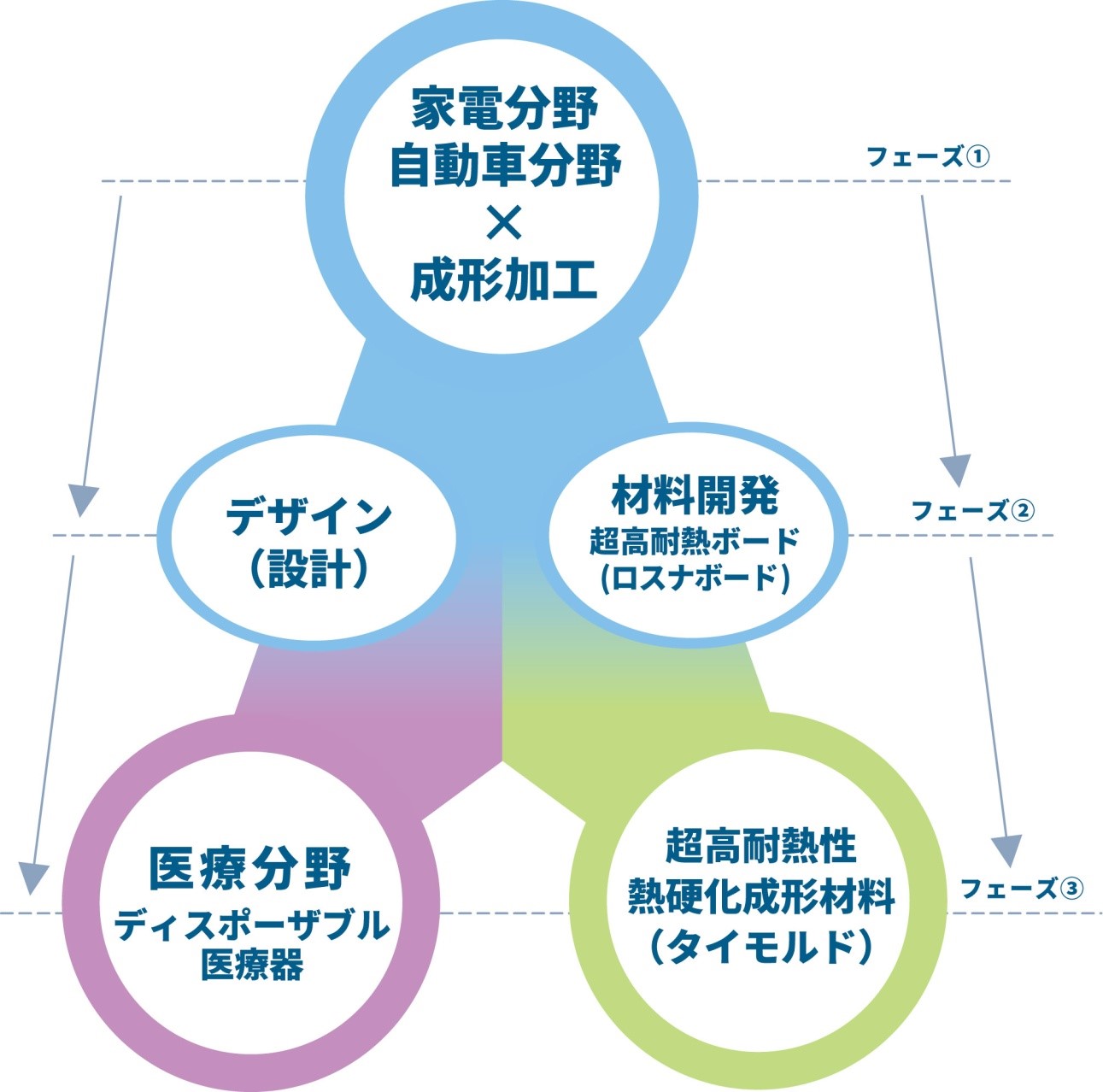
Changing the world of molded parts through automotive x molding process x material development
Nikko Kasei is a manufacturer that specializes in high-grade resin molding for precision molding of automotive parts. We do not limit ourselves to mere molding processing, but also compound higher grade thermosetting resin materials in our own technical research laboratories, aiming to offer integrated solutions from materials to molding processing. As a molding company with a thorough knowledge of compounding materials, we will continue to challenge the limits of molding processing.
≪Phase 1≫ Starting out as a molding manufacturer of automotive parts
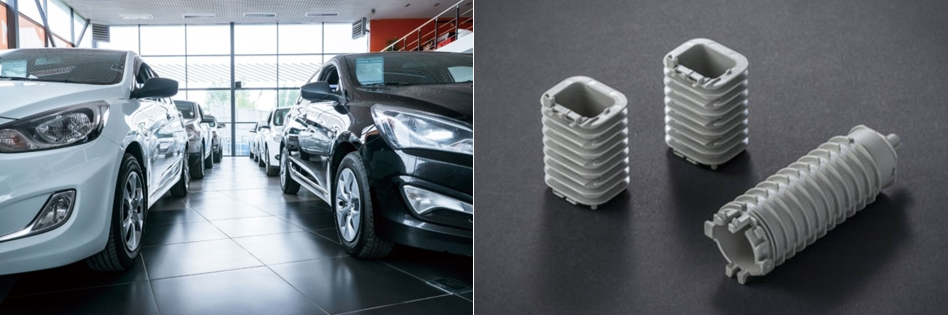
We were contracted to mold and process various internal combustion engine product parts for automobiles. Internal combustion engine parts have the strength to withstand the high temperatures of engines and to withstand high voltage without breaking down. They are called "critical safety parts" in the industry, and even one defective part out of a million could result in an accident that could affect human lives. We have studied molding technology and tooling technology for this product, which requires strict quality control, precision mold accuracy, and reliability in molding process.
≪Phase 2≫ Release of "Rosunaboard," a thermosetting resin, from the Technical Research Institute with its superior compounding technology.
≪Phase 2≫ Release of "Rosunaboard," a thermosetting resin, from the Technical Research Institute with its superior compounding technology.
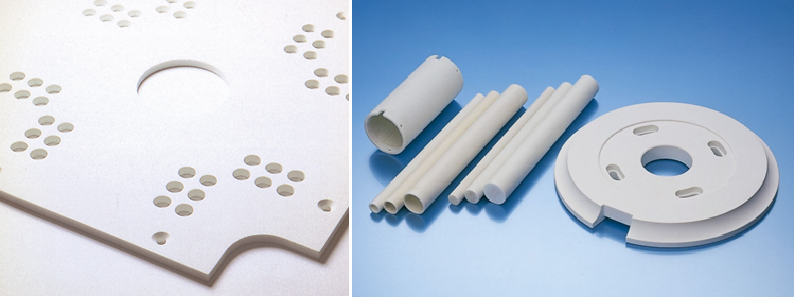
Rosuna is the highest grade of our heat-resistant board products, and is a long-selling product launched in 1982. This product is the very starting point of our company.
≪Phase 3≫ Utilizing the know-how gained from Rosunaboard, the ultra heat-resistant thermosetting molding material "Rosunamold" was born.
≪Phase 3≫ Utilizing the know-how gained from Rosunaboard, the ultra heat-resistant thermosetting molding material "Rosunamold" was born.
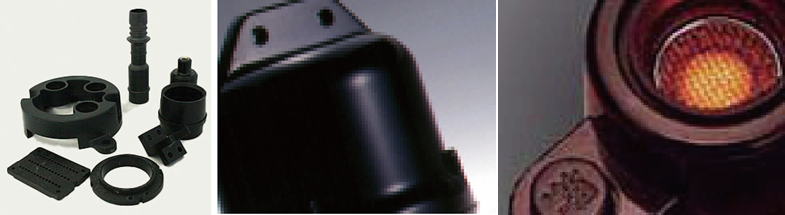
Products for use in automotive internal combustion engines. Super engineering plastic resin for high heat resistance and high strength requirements.
Rosnamold" is an innovative product that can be "molded" in a "mold" while maintaining the high heat resistance and high strength characteristics of Rosunaboard.
This is an innovative product that can be "molded" in a "mold" while maintaining the high heat resistance and high strength characteristics of Rosunaboard. In addition to injection molding, compression molding is also available.
Nikko Kasei is a manufacturer that specializes in high grade resin molding for precision molding of automotive parts. Aiming to transform itself from a contract-based company to a proposal-based company, Nikko Kasei launched its medical business in 1970. In the same year, Nikko Kasei obtained a "medical manufacturing license" and subsequently acquired medical QMS certification.
≪Phase 1≫ Contract processing of home appliances
Rosnamold" is an innovative product that can be "molded" in a "mold" while maintaining the high heat resistance and high strength characteristics of Rosunaboard.
This is an innovative product that can be "molded" in a "mold" while maintaining the high heat resistance and high strength characteristics of Rosunaboard. In addition to injection molding, compression molding is also available.
Changing the world of precision parts through medical care x molding process x design
Nikko Kasei is a manufacturer that specializes in high grade resin molding for precision molding of automotive parts. Aiming to transform itself from a contract-based company to a proposal-based company, Nikko Kasei launched its medical business in 1970. In the same year, Nikko Kasei obtained a "medical manufacturing license" and subsequently acquired medical QMS certification.
≪Phase 1≫ Contract processing of home appliances
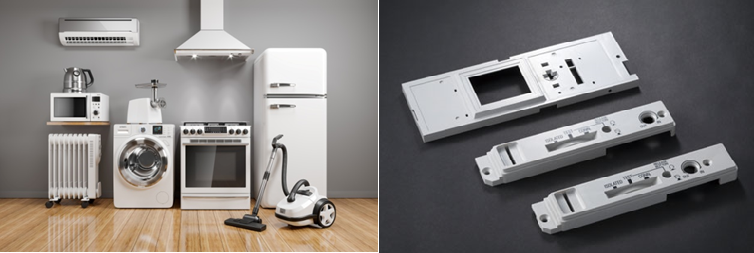
The company started as a contract molding manufacturer for various home appliances such as TVs, refrigerators, vacuum cleaners, and shavers. Design and development were done by home appliance manufacturers, and our main business was the specification and material selection of the obtained drawings, the fabrication of molds that could accurately reproduce the drawings, and the manufacturing of these products. As a manufacturer of parts processing for made-in-Japan products, we have contributed to the maintenance of parts supply in Japan, the kingdom of home appliances at that time, by implementing qualified quality control.
≪Phase 2≫ Establishment of design and design department
≪Phase 2≫ Establishment of design and design department

Not many material manufacturers have a design department. In such a situation, our great advantage is that we have an in-house design department and can deliver not only sharing materials but also making parts as a one-stop service. Sometimes, we receive orders as our customers' PB products. We are expected to provide not only materials but also design capabilities. Especially in the medical field, it is most important that the products used in the medical field fulfill their roles and are safe = the "form" of the product. Design in the medical field is the starting point for demanding precision and accuracy that can affect human lives. Thus, while being a manufacturer, we have a design department and provide services in a form close to the final product. This allows us to aim for a "B to B to C oriented manufacturing" rather than just B to B. Furthermore, we are quick to find hints for new material development and feed them back to our research and development department.
≪Phase ③≫ Disposable medical products are born as a medical venture
≪Phase ③≫ Disposable medical products are born as a medical venture
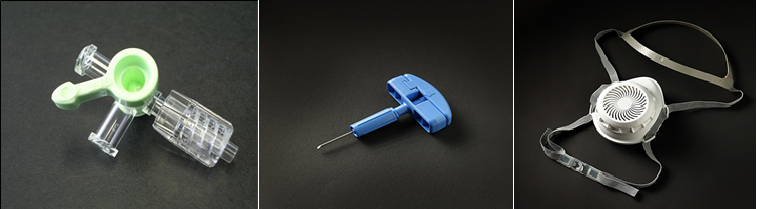
Medical Products (Disposable)" (above image, left)
The "three-way cock" is a typical product of disposable medical products. This product was created by adding design design technology to automobile molding and tooling technology.
Medical product (metal composite disposable)" (above image, center)
A new disposable product that uses metal and resin. A new disposable product that uses both metal and resin.
Medical products (composite disposable products made of different materials)" (above image, right)
A disposable product created by composite design of different materials other than resin, born through medical-engineering collaboration. A product that integrates many highly functional features
We promote joint development through "open innovation," in which we actively utilize external resources for R&D and product development, and "industry-government-academia consortiums" that include university laboratories, to develop cutting-edge and confidential projects that bring together Japanese manufacturing technologies. Furthermore, the business of disposable medical devices has developed into a medical-industrial collaboration in Corona Disaster.
Encounters with various people and companies have led to new development and research projects, and have triggered new research and challenges for our company.
The "three-way cock" is a typical product of disposable medical products. This product was created by adding design design technology to automobile molding and tooling technology.
Medical product (metal composite disposable)" (above image, center)
A new disposable product that uses metal and resin. A new disposable product that uses both metal and resin.
Medical products (composite disposable products made of different materials)" (above image, right)
A disposable product created by composite design of different materials other than resin, born through medical-engineering collaboration. A product that integrates many highly functional features
Creating next-generation technology, a new challenge
We promote joint development through "open innovation," in which we actively utilize external resources for R&D and product development, and "industry-government-academia consortiums" that include university laboratories, to develop cutting-edge and confidential projects that bring together Japanese manufacturing technologies. Furthermore, the business of disposable medical devices has developed into a medical-industrial collaboration in Corona Disaster.
Encounters with various people and companies have led to new development and research projects, and have triggered new research and challenges for our company.
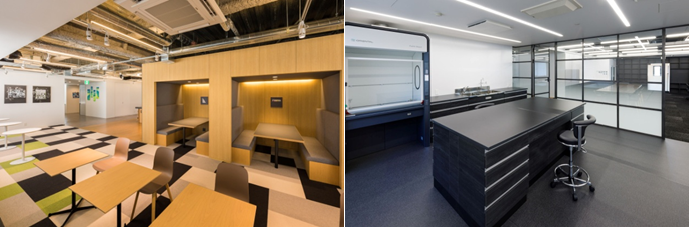
Technical innovation by utilizing partnerships with specialized organizations. Promote contributions to the local community.
Nikko Chemical has two research centers in Osaka and Shiga that support development technology. The Osaka facility is responsible for development in the medical and biotechnology fields, while the Shiga facility is in charge of materials development in a variety of fields. While refining our own core technologies, we conduct development through joint research in collaboration with public R&D institutions, major companies, and local universities in each region.
Such community-based research activities have been recognized,
In 2018, we were named a "Regional Future Leading Company" by the Ministry of Economy, Trade and Industry,
In 2019, we were selected as one of the "300 Small and Medium Enterprises" by the Small and Medium Enterprise Agency,
Osaka Prefecture's "Osaka Monozukuri Excellent Company Award" in 2019,
In 2021, we were selected as one of the "Excellent Health Management Corporations 2021" by the Ministry of Economy, Trade and Industry.
We will continue to contribute to the community and society and aim to be a "future-oriented company" capable of further technological innovation.
Please send us your inquiries by clicking the "Contact Us" button below.